Mastering Quality Management System Principles for Business Success
Making decisions based on evidence not only minimizes risks but also carves a path toward strategic operational excellence.
Published on:
September 05 2024Mastering Quality Management System Principles for Business Success
The success of any organization hinges on its ability to consistently deliver value to its customers. Central to this objective is the adoption of a robust Quality Management System (QMS) rooted in universally accepted principles. With customer satisfaction at the forefront, a QMS orchestrates every organizational activity to meet customer needs and exceed expectations.
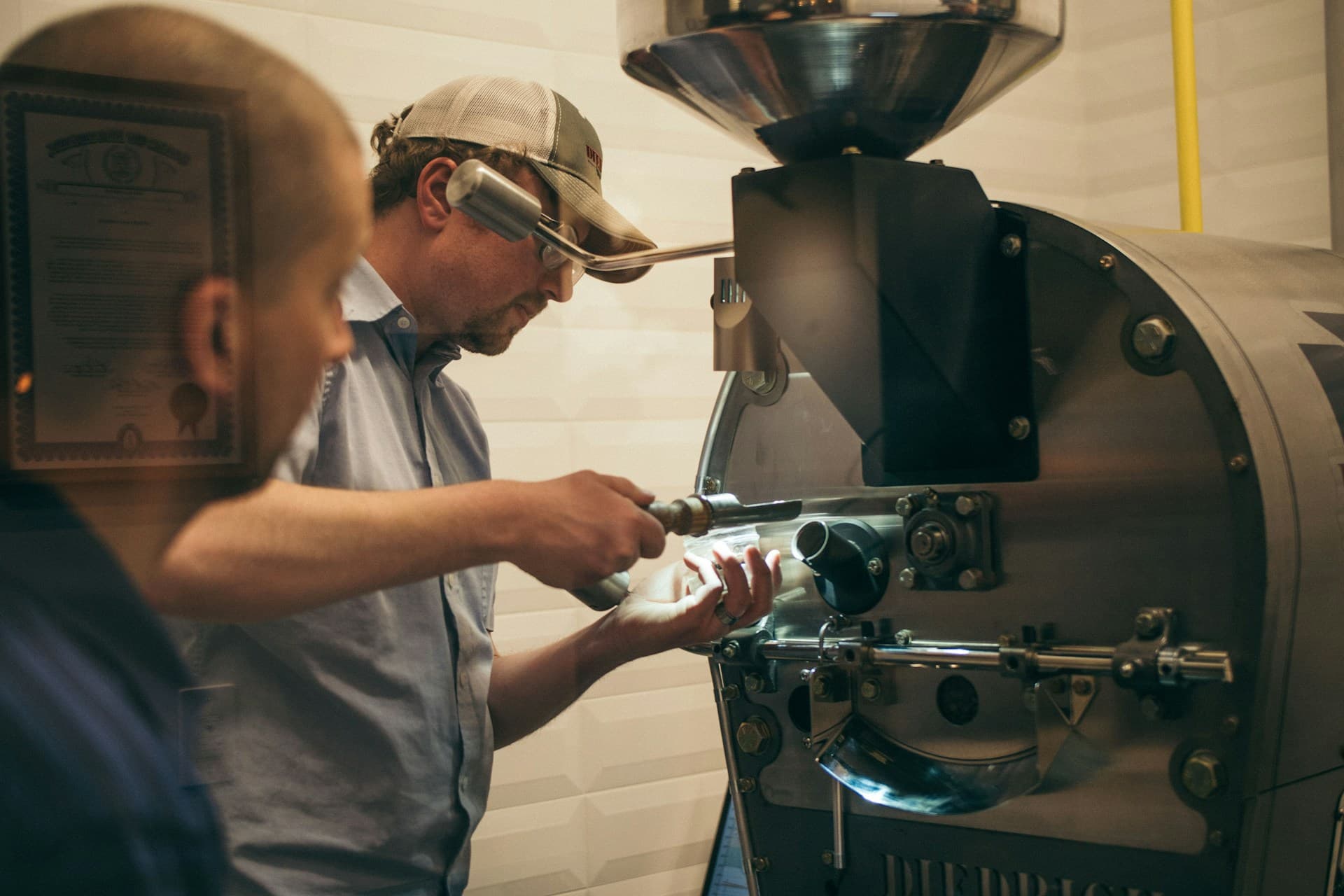
Leadership is another cornerstone of any effective QMS, providing direction and aligning the various components of the organization towards quality objectives. Moreover, engaging people at every level ensures a collaborative environment where every team member contributes to the organization's quality goals.
Incorporating a process approach into organizational operations streamlines activities, turning inputs into valuable outputs efficiently. Continuous improvement, meanwhile, keeps the organization agile and responsive to changes, ensuring long-term relevance and competitiveness.
Making decisions based on evidence not only minimizes risks but also carves a path toward strategic operational excellence. Managing relationships, including those with vendors and partners, forms a supportive network that complements internal structures and resources. Furthermore, adherence to ISO 9001 standards sets a global benchmark for QMS implementation, fostering an environment of trust and reliability in international business dealings.
To navigate the complex landscape of regulatory compliance, understanding the nuances of QMS is indispensable for organizations aspiring to operate efficiently and lawfully in their respective markets. This foundational mastery forms the backbone of a resilient, quality-centric organization.
Designing and Documenting Your QMS
A Quality Management System (QMS) thrives on clarity and precision, starting with defining quality objectives and policies. These objectives articulate the performance metrics and goals the organization aims to achieve, while policies provide the framework for decision-making within the QMS structure.
Document Control within QMS
Exerting control over documents preserves the integrity of a QMS. Organizations benefit from systems that ensure documents are approved, reviewed, and updated by designated personnel. Moreover, the process ensures that obsolete documents are promptly removed from circulation, mitigating the risk of misinformation. Document control mechanisms safeguard the consistency of a QMS, which in turn, supports its effectiveness and compliance with standards.
Importance of Accurate Documentation
Accurate documentation underpins the operational efficacy of a QMS. Comprehensive record-keeping enables tracking of quality processes, provides evidence of compliance, and informs decision-making.
Best Practices for Document Management
- Efficiency in document management is achieved through the adoption of best practices which include embracing digital platforms for easier access, implementing a structured filing system, ensuring version control, and allowing for traceability of document changes.
- Such practices ensure documents are current and readily accessible to authorized personnel, enhancing the responsiveness of the QMS.
The Significance of Process Documentation in Product and Service Quality
Documenting processes is not merely a procedural necessity; it is instrumental in ensuring consistent quality of products and services. Detailed process documentation acts as a guide for operations, aids in training new employees, and serves as a reference for process improvement initiatives. Furthermore, it provides a means for process verification and validation, playing a critical role in demonstrating the QMS's capability in maintaining product and service excellence.
- Structured documentation serves as a guideline for quality excellence.
- Accurate records contribute to efficient traceability and accountability.
- Regularly updated documents reflect a dynamic and adaptable QMS.
Processes and Continuous Improvement in a Quality Management System
A Quality Management System encompasses various elements, with processes being among the most critical. Defined sequences and procedures guide an organization, aiming for excellence and satisfying customer requirements. Implementing a process approach ensures that activities and resources are managed as interconnected processes, creating a more harmonious workflow and leading to improved efficiency and effectiveness.
The Role of Processes in a QMS
Processes serve as the operational backbone of a QMS. They convert inputs into outputs efficiently, directly impacting an organization's ability to meet both quality and performance targets. Structuring processes to align with quality objectives ensures that they advance the company's vision for quality in every task performed.
Continuous Improvement Methodologies
Evolving a QMS is facilitated by adopting continuous improvement methodologies. These strategies foster a proactive culture, constantly seeking opportunities to enhance performance, reduce waste, and innovate.
- Total Quality Management (TQM): This holistic approach focuses on long-term success through customer satisfaction. In TQM, employees at all levels actively participate in improving processes, products, and services.
- Six Sigma: With a strong emphasis on data and statistical analysis, Six Sigma aims to minimize defects and variability in manufacturing and business processes, pushing for near perfection.
Adopting these methodologies will lead to significant transformations in an organization's operational health and quality output.
The Process Approach to Managing Activities and Resources
Integration of a process approach into a QMS emphasizes the importance of understanding and managing processes as interrelated systems that function cohesively. This perspective not only provides clearer insight into process efficiency but also assists in prioritizing process improvement opportunities, which is conducive to achieving strategic goals.
Establishing a Culture of Quality and Improvement
Achieving and maintaining high quality standards demands building a culture that values quality and continuous improvement. It requires employees' unwavering commitment at all levels, from top management fostering an environment where quality becomes a shared value, to the operational staff engaging in day-to-day quality practices. This company-wide dedication is what ensures the longevity and success of a QMS.
Quality Control and Quality Assurance: Navigating their Intersections and Differences
To delineate between quality control (QC) and quality assurance (QA), consider QC as the detection mechanism in a quality management system, focusing on identifying defects in products. QA, conversely, functions as a preventive measure, implementing a process-oriented approach designed to avert the occurrence of errors. Both elements coalesce to form a comprehensive approach to quality management, yet each serves a distinctive role in the pursuit of excellence.
Techniques for Quality Control
Diverse industries employ varied QC techniques to ensure their products meet established specifications. In manufacturing, statistical process control (SPC) monitors and controls the production process through data analysis, revealing trends that may indicate potential issues. Non-destructive testing (NDT) methods, such as ultrasonics and radiography, permit the examination of materials without altering their form, ensuring integrity and safety.
Service industries, where tangibility is less pronounced, nonetheless utilize QC methods tailored to their needs. Mystery shopping, for instance, assesses the service delivery and environment by simulating customer interactions. Service performance metrics, like wait times and customer satisfaction scores, create a data-driven framework for evaluating and enhancing service quality.
Ensuring Quality Assurance
- Developing comprehensive protocols, policies, and procedures lays the groundwork for consistent quality assurance processes.
- Employee training programs, pivotal in conveying necessary skills and fostering a quality-oriented mindset, must undergo regular updates to reflect evolving standards and practices.
- Regular internal audits and external certifications against recognized standards, such as ISO 9001, serve as benchmarks for a company's commitment to quality assurance.
Engaging robust QA practices not only upholds product and service quality but also signals to customers a dedication to exceeding their expectations. This aligns the perception of a brand with reliability and value, fostering customer loyalty.
Assessing Risks and Performance in Your Quality Management System
Within the structure of a Quality Management System (QMS), risk management transcends mere compliance; its integration ensures resilience and sustainability. A robust QMS proactively identifies potential risks to product quality and customer satisfaction. This proactive stance not only anticipates issues but also prepares the organization to respond promptly.
Key to a QMS's efficacy is the adoption of performance measurement, which deploys an array of indicators. These indicators, often quantifiable, such as defect rates, turnaround time, and customer satisfaction scores, offer organizations a lens through which to examine their quality processes objectively.
How to Define and Measure Performance
Performance in a QMS is not a guessing game. Clear definition and consistent measurement of performance drive informed decision-making. Stakeholders need to collaborate in identifying what success looks like, which tends to involve establishing benchmarks, setting targets, and identifying relevant metrics aligned with organizational goals.
Once organizations define performance parameters, regular measurement becomes routine. Using tools like balanced scorecards or Six Sigma methodologies can bring clarity and focus to this step. Measurement, in this context, encompasses both process-oriented metrics and outcome-oriented indicators, providing a holistic view of organizational performance.
Using Data to Drive QMS Effectiveness
Data forms the bedrock of any decision-making process in a QMS. Organizations should leverage data analytics to scrutinize performance and identify trends. With this approach, organizations can visualize the quality landscape, identifying areas for improvement, predicting challenges, and crafting strategic responses. Moreover, data-driven decisions solidify the objective nature of quality management, anchoring QMS initiatives in concrete evidence rather than subjective judgment.
Risk-Based Thinking in QMS
Risk-based thinking, a principle embedded in modern QMS frameworks, necessitates a proactive approach to managing uncertainties. Unlike reactive risk management, which addresses risks after their materialization, risk-based thinking encourages foresight. This foresight manifests in preventive actions, which are strategically implemented to mitigate risks before they evolve into issues.
By integrating risk-based thinking into the QMS, organizations cultivate a resilience that is crucial in today’s volatile business environment. This approach not only safeguards the quality of products and services but also enhances the organization's capacity to adapt and thrive amidst change.
Conclusion: The Integral Role of QMS in Achieving Business Success
In conclusion, a well-implemented Quality Management System (QMS) is not merely a tool for ensuring compliance; it is a cornerstone of organizational success. It provides a structured approach to managing quality, from the initial design of processes and documentation to continuous improvement and risk management. By embracing the principles and methodologies discussed, organizations can achieve operational excellence, enhance customer satisfaction, and secure a competitive edge in their industry.
Adopting a QMS that aligns with international standards like ISO 9001 further solidifies an organization's commitment to quality, opening doors to global opportunities and fostering long-term success. Ultimately, the pursuit of quality through a robust QMS is not just about meeting standards—it's about exceeding them, creating value for customers, and driving sustained business growth.